
I suggest doing this at least once before doing any work, just to get a feel for it. Once you've placed the pipe the correct distance into the forge and applied the refractory, being careful not to obstruct the airflow and to leave a working area big enough for the work you plan to do, it's tome to test-fire it. One pic's just the forge itself with nothing added, the other's a pic with the empty refractory pot in for a sense of scale.Īlso known as lighting the forge. The refractory should be fairly thin on the bottom, thickish at the bottom of the walls, getting thinner (but not too thin) towards the top. I took these the afternoon after i fired it up so the refractory's stained and sootied but i think they get the point across. By demand, popular or not, here's some pics on how i added the refractory. Follow the instructions and only fire up the forge when the stuff's ready. Mine needed to be fired immediately after being applied, so no pictures there. Allow the refractory to set as per the instructions that should have come with it. Make sure that no steel peeks through the refractory.

Put about half an inch on the bottom and build it up round the sides leave a working area about 8 to 10 inches wide and 4 deep at least. Mine was rated to 1250 degrees centigrade, lower than I wanted but still plenty high enough.

Chances are it'll do this at the worst possible moment and carry a cargo of hot coal into your eye. Whatever you do, don't use something that expands too much. The Refractory reflects the heat back up into the fire, making it more efficient and less likely to melt its way out the bottom of the.cake tin (shudder) It's going to get Seriously hard. "THE FIERCER THE HEAT, THE HARDER IT GETS!" bragged my fire cement. Make sure the pipe doesn't go too far in or not far enough in. SO: this step's instructions: Through Fair means or Foul, Make a hole big enough to fit the pipe through. "It's only thin steel, what can possibly go wrong?" I spent something like 40 minutes getting a hole big enough to put the pipe through. To get the air into the forge, we need a hole through which we can out a pipe.
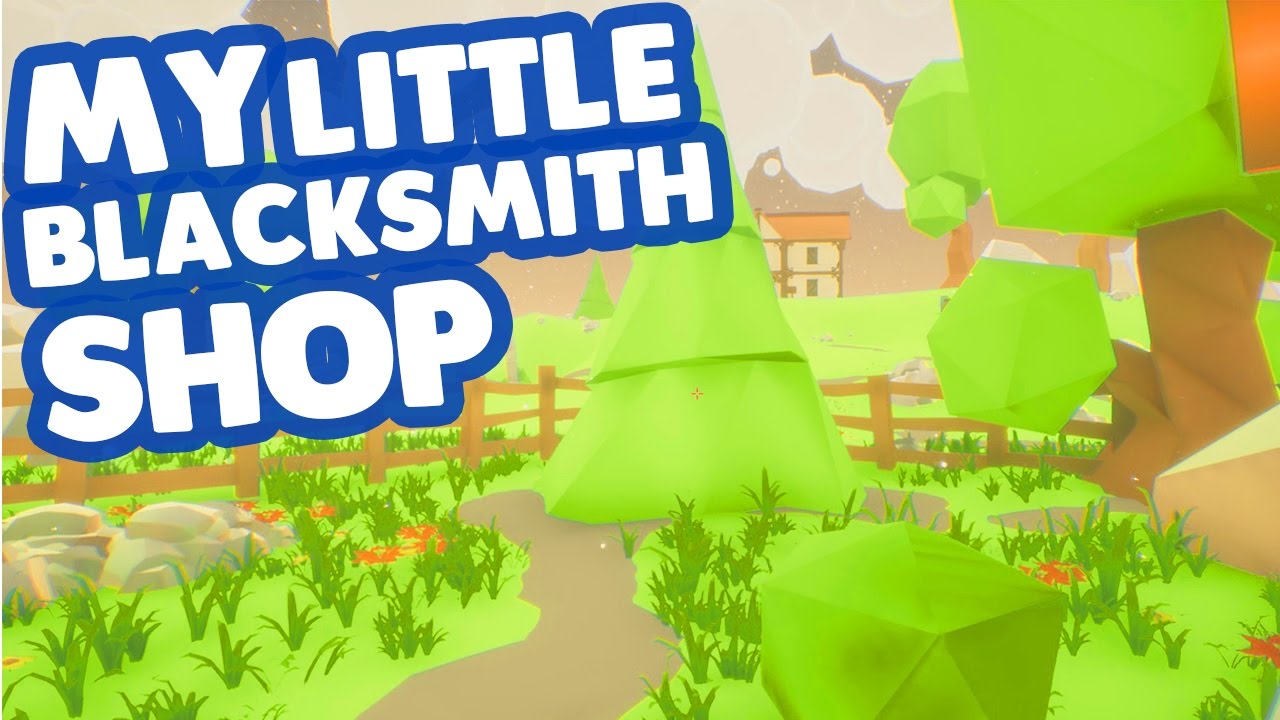
The first thing we need to consider when building a forge is the ariflow. I never once thought i'd be making a forge in something that vould have been used to hold cakes but it worked really well. I ended up using a 12 inch stainless steel cake tin. I WANTED to use a wheel from a car to do this but i couldn't be bothered going all the way to a place to get it only to carry it home and eventually set it on fire, so i looked closer to home.
